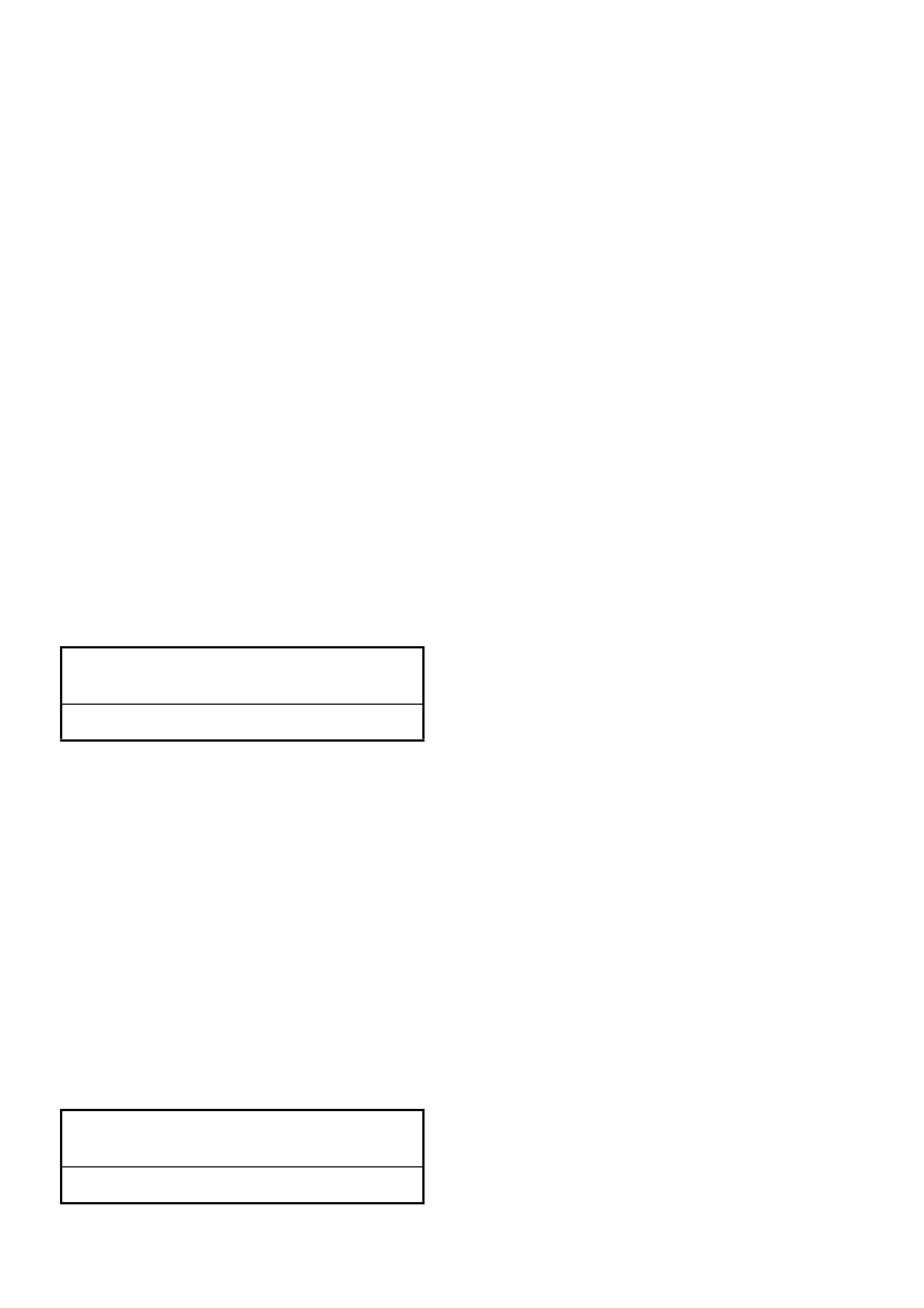
2.3 TRANSMISSION COOLER REVERSE FLUSH AND FLOW RATE CHECK –
ALL ENGINES
It is essential that a reverse flush and oil cooler flow rate check is performed, after ANY of the following
situations:
• Transmission replacement.
• If fluid contamination is suspected.
• Whenever the oil pump and/or torque converter is replaced.
NOTE: The reverse flush must be completed prior to conducting a flow rate check.
REVERSE FLUSH
The rec ommended procedur e f or rever se flushing the trans mission c ooler and lines , par ticular ly after an overhauled
or replaced transmission has been installed into the vehicle, is as follows:
1. Disconnect both cooler lines at the transmission and at the radiator cooler. Use a back-up spanner to hold
unions, to prevent damage to the lines.
2. Caref ully check the cooler inlet fitting (lower right hand s ide) to see whether any material is evident at this point.
If so, dis lodge and rem ove with a suitable tool and/or com pr essed air blown in the reverse direc tion through the
cooler.
3. Using a commercially available pressure spray gun and clean solvent, such as white spirit:
a. Back flush through both cooler lines.
b. Back flush through the cooler/s, including the external cooler (if fitted).
c. Blow compressed air through return and inlet pipes to remove solvent.
d. Flush pipes with transmission fluid.
4. Reconnect cooler lines to the transmission and cooler but leave the cooler return line to transmission
connection open.
5. Conduct a flow rate test as described below, to ensure that any restriction has been cleared.
6. If flow rate is satisfactory, reconnect the return line to the transmission, tightening all fittings to the specified
torque.
OIL COOLER PIPES TO
TRANSMISSION FITTING 35 – 41 Nm
TORQUE SPECIFICATION (All Engines)
OIL COOLER HOSE TO RADIATOR 25 – 30 Nm
PIPE TORQUE SPECIFICATION (V6 Engines Only)
7. Lower vehicle and check fluid level as detailed in 2.1 FLUID LEVEL CHECK, in this Section.
FLOW RATE CHECK
CAUTION: Do not run engine any longer than absolutely necessary, as too low a fluid level can cause
aeration and foaming.
1. When installing the transmission assembly, leave the cooler return line disconnected from the transmission
(upper fitting).
2. Ensure that the fluid level is to the recommended level, as detailed in 2.1 FLUID LEVEL CHECK, in this
Section.
3. Place a container underneath the disconnected cooler line.
4. With the selector lever in the Neutral position, start the engine and observe the fluid flow into the container, after
all air bubbles have ceased and a steady flow is evident. Measure the flow rate.
Result: The fluid flow rate should be approximately 0.7 litre in a 20 second period, WITH COLD AUTOMATIC
TRANSMISSIO N FLUID (AT F). W ith ATF at nor mal operating tem perature (86 – 93 °C), the f low rate will increase
and should be approximately 1.2 litres in a 20 second period.
If the f low rate is less than this s pecification, the s ource of the restriction m ust be located and rect ified. Possibilities
are either radiator tank cooler, faulty flexible hoses and/or external cooler (if fitted).
5. Reinstall the cooler return line to the transmission and tighten all fittings to the specified torque.
OIL COOLER PIPES TO
TRANSMISSION FITTING 35 – 41 Nm
TORQUE SPECIFICATION (All Engines)
OIL COOLER HOSE TO RADIATOR 25 – 30 Nm
PIPE TORQUE SPECIFICATION (V6 Engines Only)