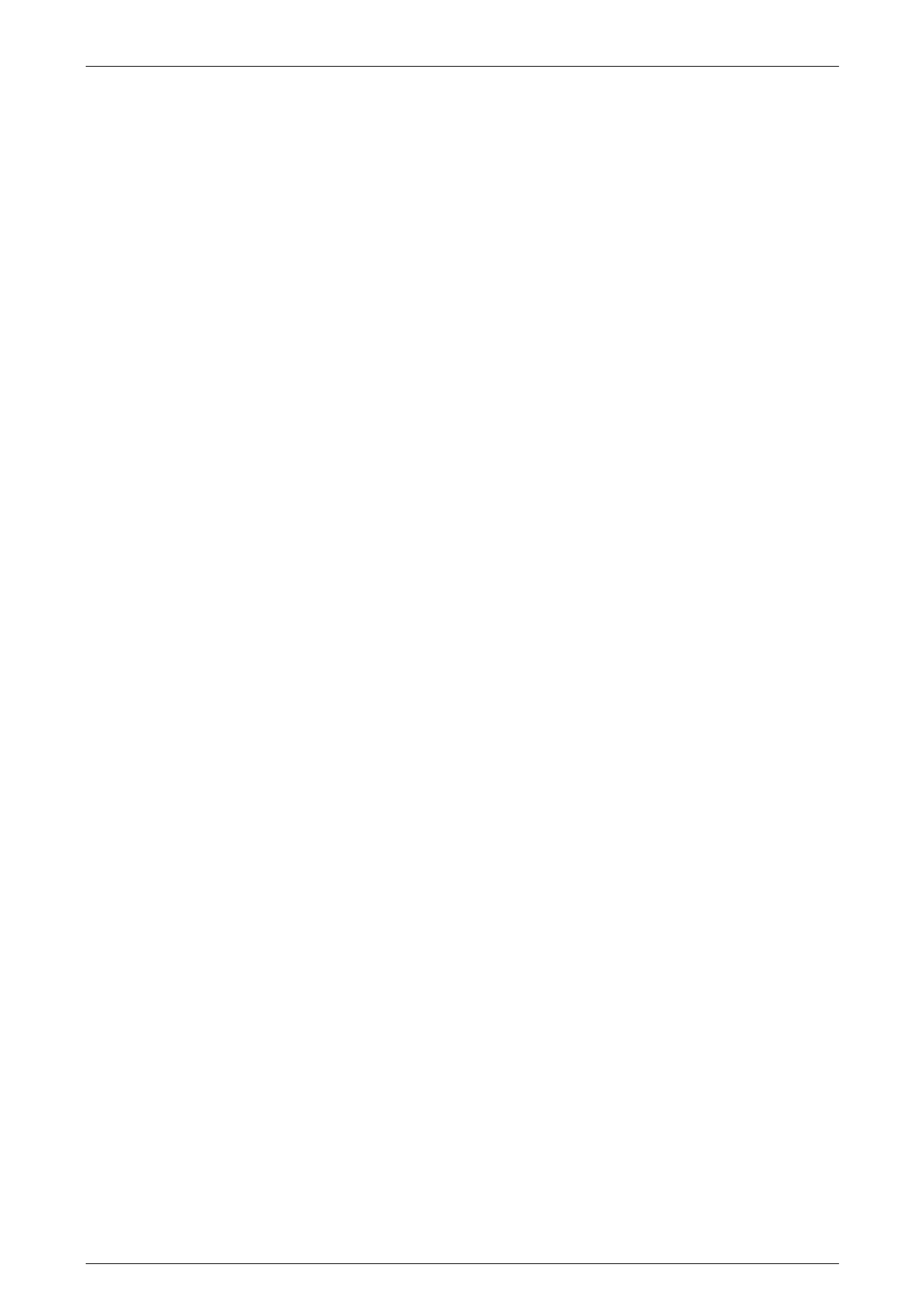
ABS-TCS – GEN III V8 AWD Page 5B7–3
Page 5B7–3
Conditions for Running DTC .............................................................................................................................. 49
DTC C0035, C0040, C0045 and C0050........................................................................................................... 49
DTC C0036, C0041, C0046 and C0051........................................................................................................... 49
Conditions for Setting DTC................................................................................................................................. 50
DTC C0035, C0040, C0045 or C0050.............................................................................................................. 50
DTC C0036, C0041, C0046 and C0051........................................................................................................... 50
Action Taken when the DTC Sets....................................................................................................................... 50
Conditions for Clearing the DTC........................................................................................................................ 50
Test Description................................................................................................................................................... 50
DTC C0035, C0036, C0040, C0041, C0045, C0046, C0050 or C0051 Diagnostic Table ................................... 51
8.3 DTC C0110 – Hydraulic Modulator Pump Motor Circuit ................................................................................... 53
DTC Description................................................................................................................................................... 53
Circuit Description............................................................................................................................................... 53
Additional Information......................................................................................................................................... 53
Conditions for Running the DTC........................................................................................................................ 53
Conditions for Setting the DTC .......................................................................................................................... 53
Action Taken When the DTC Sets ...................................................................................................................... 53
Conditions for Clearing the DTC........................................................................................................................ 53
Test Description................................................................................................................................................... 53
DTC C0110 Diagnostic Table .............................................................................................................................. 54
8.4 DTC C0121 – ECU Internal Valve Relay.............................................................................................................. 55
DTC Description................................................................................................................................................... 55
Circuit Description............................................................................................................................................... 55
Additional Information......................................................................................................................................... 55
Conditions for Running the DTC........................................................................................................................ 55
Conditions for Setting the DTC .......................................................................................................................... 55
Action Taken When the DTC Sets ...................................................................................................................... 55
Conditions for Clearing the DTC........................................................................................................................ 55
Test Description................................................................................................................................................... 55
DTC C0121 Diagnostic Table .............................................................................................................................. 56
8.5 DTC C0161 – Brake Sw itch Circuit ..................................................................................................................... 57
DTC Description................................................................................................................................................... 57
Circuit Description............................................................................................................................................... 57
Additional Information......................................................................................................................................... 57
Conditions for Running the DTC........................................................................................................................ 57
Conditions for Setting the DTC .......................................................................................................................... 57
Action Taken When the DTC Sets ...................................................................................................................... 57
Conditions for Clearing the DTC........................................................................................................................ 57
Test Description................................................................................................................................................... 57
DTC C0161 Diagnostic Table .............................................................................................................................. 58
8.6 DTC C0191 or C0192 – Longitudinal Acceleration Sensor Signal Circuit....................................................... 59
DTC Description................................................................................................................................................... 59
Circuit Description............................................................................................................................................... 59
Additional information......................................................................................................................................... 59
Conditions for Running the DTC........................................................................................................................ 59
Conditions for Setting the DTC .......................................................................................................................... 59
DTC C0191 ...................................................................................................................................................... 59
DTC C0192 ...................................................................................................................................................... 59
Action Taken When the DTC Sets ...................................................................................................................... 59
Conditions for Clearing the DTC........................................................................................................................ 60
Test Description................................................................................................................................................... 60
DTC C0191 or C0192 Diagnostic Table .............................................................................................................. 60
8.7 DTC C0245 – Wheel Speed Sensor Output........................................................................................................ 62
DTC Description................................................................................................................................................... 62
Circuit Description............................................................................................................................................... 62
Additional Information......................................................................................................................................... 62
Conditions for Running the DTC........................................................................................................................ 62
Conditions for Setting the DTC .......................................................................................................................... 62