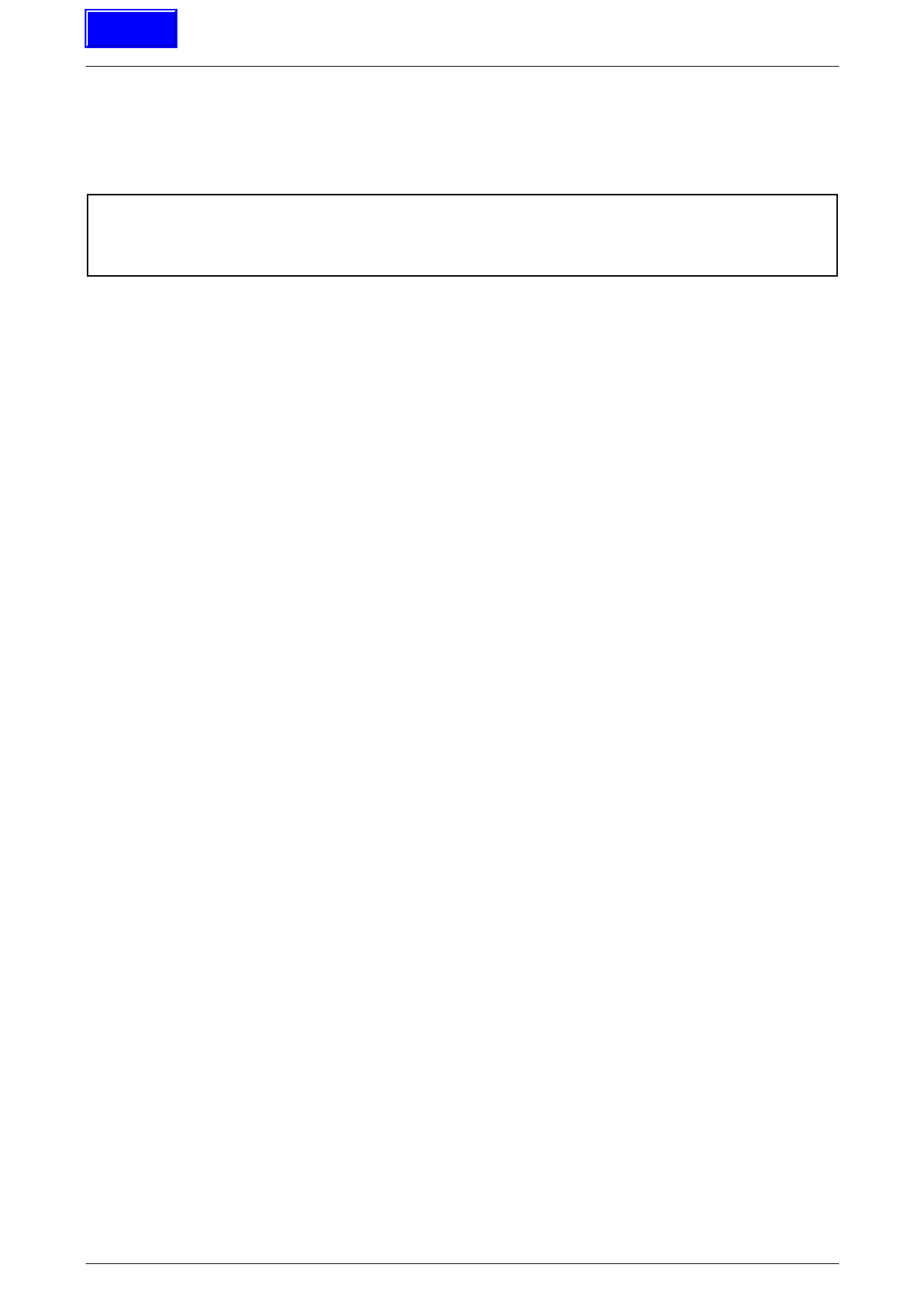
Engine Management – V6 – General Information Page 6C1-1–1
Section 6C1-1
Engine Management V6 – General Information
ATTENTION
Before performing any service operation or other procedure described in this Section, refer to Section 00
Warnings, Cautions and Notes for correct workshop practices with regard to safety and / or property damage.
1 General Information ...............................................................................................................................3
1.1 Introduction............................................................................................................................................................ 3
1.2 Emission Control................................................................................................................................................... 4
Euro 2 Emissions Standards ................................................................................................................................ 4
2 Component Locations ...........................................................................................................................5
2.1 Cylinder Numbering............................................................................................................................................... 5
2.2 Engine Compartment............................................................................................................................................. 6
2.3 Engine..................................................................................................................................................................... 7
Alloytech................................................................................................................................................................. 7
Alloytech 190.......................................................................................................................................................... 8
All Engines ............................................................................................................................................................. 9
2.4 Manual Transmission .......................................................................................................................................... 10
2.5 Interior .................................................................................................................................................................. 11
3 System Operation.................................................................................................................................12
3.1 Fuel Delivery System........................................................................................................................................... 12
Fuel System Pressure ......................................................................................................................................... 12
Fuel Injection System.......................................................................................................................................... 13
Short Term Fuel Trim....................................................................................................................................... 13
Long Term Fuel Trim........................................................................................................................................ 13
3.2 Air / Fuel Control System.................................................................................................................................... 14
Starting Mode....................................................................................................................................................... 14
Run Mode ............................................................................................................................................................. 14
Acceleration Mode............................................................................................................................................ 14
Deceleration Mode........................................................................................................................................... 14
Fuel Shut-off Mode........................................................................................................................................... 14
Battery Voltage Correction Mode..................................................................................................................... 15
Limp Mode ....................................................................................................................................................... 15
Engine Protection Mode................................................................................................................................... 15
Clear Flood Mode............................................................................................................................................. 15
3.3 Ignition Control System ...................................................................................................................................... 16
3.4 Starter Motor Operation ...................................................................................................................................... 17
Auto Start Feature................................................................................................................................................ 17
Clutch Pedal Position Switch.............................................................................................................................. 17
3.5 Throttle Actuator Control System ...................................................................................................................... 18
Description........................................................................................................................................................... 18
Throttle Body Relearn Procedure....................................................................................................................... 19
TAC System Default Actions / Reduce Power Modes....................................................................................... 19
Forced Engine Shutdown.................................................................................................................................... 19
3.6 Camshaft Position Actuator Control System .................................................................................................... 20
Operation.............................................................................................................................................................. 21
Variable Valve Timing Phases ......................................................................................................................... 21
3.7 Cruise Control System ........................................................................................................................................ 23
3.8 Brake Torque Management................................................................................................................................. 24
Page 6C1-1–1