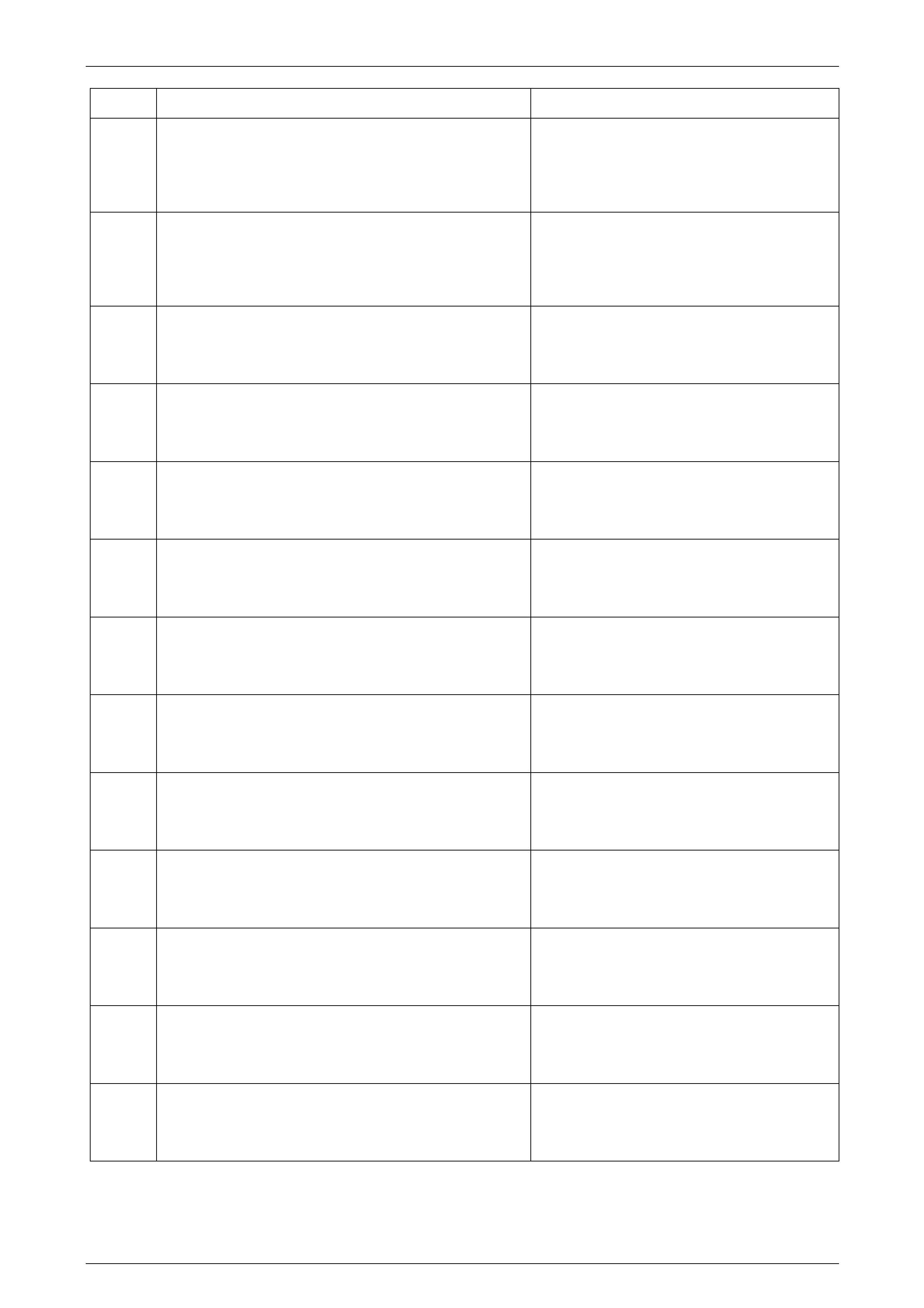
Engine Management – V6 – Diagnostics Page 6C1-2–66
Page 6C1-2–66
DTC Description Diagnostic Table
P2297 O2 Sensor Range / Performance During Deceleration Fuel
Cutoff (Bank 1, Sensor 1)
5.35 DTC P0130 to P0132, P0135, P0137,
P0138, P0140, P0141, P0150 to P0152,
P0155, P0157, P0158, P0160, P0161,
P2243, P2247, P2270 to P2273, P2297,
P2298 – O2 Sensor Reference Circuit
P2298 O2 Sensor Range / Performance During Deceleration Fuel
Cutoff (Bank 2, Sensor 1)
5.35 DTC P0130 to P0132, P0135, P0137,
P0138, P0140, P0141, P0150 to P0152,
P0155, P0157, P0158, P0160, P0161,
P2243, P2247, P2270 to P2273, P2297,
P2298 – O2 Sensor Reference Circuit
P2300 Ignition Coil Cylinder 1 Circuit Low Voltage 5.28 DTC P0351 to P0356, P2300, P2301,
P2303, P2304, P2306, P2307, P2309,
P2310, P2312, P2313, P2315 and P2316 –
Ignition Coil Control Circuit
P2301 Ignition Coil Cylinder 1 Circuit High Voltage 5.28 DTC P0351 to P0356, P2300, P2301,
P2303, P2304, P2306, P2307, P2309,
P2310, P2312, P2313, P2315 and P2316 –
Ignition Coil Control Circuit
P2303 Ignition Coil Cylinder 2 Circuit Low Voltage 5.28 DTC P0351 to P0356, P2300, P2301,
P2303, P2304, P2306, P2307, P2309,
P2310, P2312, P2313, P2315 and P2316 –
Ignition Coil Control Circuit
P2304 Ignition Coil Cylinder 2 Circuit High Voltage 5.28 DTC P0351 to P0356, P2300, P2301,
P2303, P2304, P2306, P2307, P2309,
P2310, P2312, P2313, P2315 and P2316 –
Ignition Coil Control Circuit
P2306 Ignition Coil Cylinder 3 Circuit Low Voltage 5.28 DTC P0351 to P0356, P2300, P2301,
P2303, P2304, P2306, P2307, P2309,
P2310, P2312, P2313, P2315 and P2316 –
Ignition Coil Control Circuit
P2307 Ignition Coil Cylinder 3 Circuit High Voltage 5.28 DTC P0351 to P0356, P2300, P2301,
P2303, P2304, P2306, P2307, P2309,
P2310, P2312, P2313, P2315 and P2316 –
Ignition Coil Control Circuit
P2309 Ignition Coil Cylinder 4 Circuit Low Voltage 5.28 DTC P0351 to P0356, P2300, P2301,
P2303, P2304, P2306, P2307, P2309,
P2310, P2312, P2313, P2315 and P2316 –
Ignition Coil Control Circuit
P2310 Ignition Coil Cylinder 4 Circuit High Voltage 5.28 DTC P0351 to P0356, P2300, P2301,
P2303, P2304, P2306, P2307, P2309,
P2310, P2312, P2313, P2315 and P2316 –
Ignition Coil Control Circuit
P2312 Ignition Coil Cylinder 5 Circuit Low Voltage 5.28 DTC P0351 to P0356, P2300, P2301,
P2303, P2304, P2306, P2307, P2309,
P2310, P2312, P2313, P2315 and P2316 –
Ignition Coil Control Circuit
P2313 Ignition Coil Cylinder 5 Circuit High Voltage 5.28 DTC P0351 to P0356, P2300, P2301,
P2303, P2304, P2306, P2307, P2309,
P2310, P2312, P2313, P2315 and P2316 –
Ignition Coil Control Circuit
P2315 Ignition Coil Cylinder 6 Circuit Low Voltage 5.28 DTC P0351 to P0356, P2300, P2301,
P2303, P2304, P2306, P2307, P2309,
P2310, P2312, P2313, P2315 and P2316 –
Ignition Coil Control Circuit