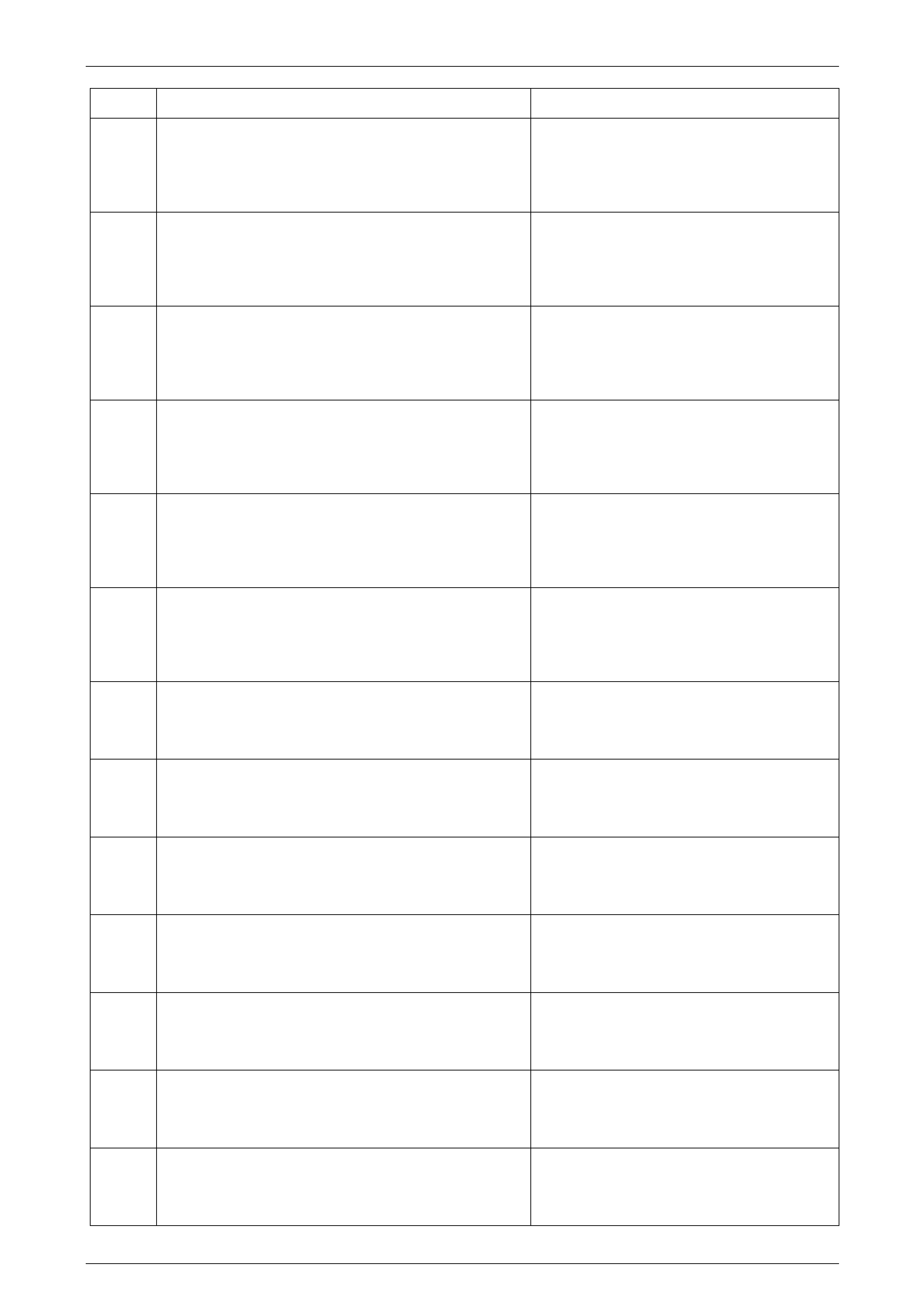
Engine Management – V6 – Diagnostics Page 6C1-2–78
DTC Description Diagnostic Table
P2270 O2 Sensor Lean / Rich Switch Signal Malfunction (Bank 1,
Sensor 2) 6.12 DTC P0130, P0131, P0132, P0135,
P0137, P0138, P0140, P0141, P0150
P0151, P0152, P0155, P0157, P0158,
P0160, P0161, P2243, P2247, P2270,
P2271, P2272, P2273, P2297 or P2298
P2271 O2 Sensor Rich / Lean Switch Signal Malfunction (Bank 1,
Sensor 2) 6.12 DTC P0130, P0131, P0132, P0135,
P0137, P0138, P0140, P0141, P0150
P0151, P0152, P0155, P0157, P0158,
P0160, P0161, P2243, P2247, P2270,
P2271, P2272, P2273, P2297 or P2298
P2272 O2 Sensor Lean / Rich Switch Signal Malfunction (Bank 2,
Sensor 2) 6.12 DTC P0130, P0131, P0132, P0135,
P0137, P0138, P0140, P0141, P0150
P0151, P0152, P0155, P0157, P0158,
P0160, P0161, P2243, P2247, P2270,
P2271, P2272, P2273, P2297 or P2298
P2273 O2 Sensor Rich / Lean Switch Signal Malfunction (Bank 2,
Sensor 2) 6.12 DTC P0130, P0131, P0132, P0135,
P0137, P0138, P0140, P0141, P0150
P0151, P0152, P0155, P0157, P0158,
P0160, P0161, P2243, P2247, P2270,
P2271, P2272, P2273, P2297 or P2298
P2297 O2 Sensor Range / Performance During Deceleration Fuel
Cutoff (Bank 1, Sensor 1) 6.12 DTC P0130, P0131, P0132, P0135,
P0137, P0138, P0140, P0141, P0150
P0151, P0152, P0155, P0157, P0158,
P0160, P0161, P2243, P2247, P2270,
P2271, P2272, P2273, P2297 or P2298
P2298 O2 Sensor Range / Performance During Deceleration Fuel
Cutoff (Bank 2, Sensor 1) 6.12 DTC P0130, P0131, P0132, P0135,
P0137, P0138, P0140, P0141, P0150
P0151, P0152, P0155, P0157, P0158,
P0160, P0161, P2243, P2247, P2270,
P2271, P2272, P2273, P2297 or P2298
P2300 Ignition Coil Cylinder 1 Circuit Low Voltage 6.24 DTC P0351, P0352, P0353, P0354,
P0355, P0356, P2300, P2301, P2303,
P2304, P2306, P2307, P2309, P2310,
P2312, P2313, P2315 or P2316
P2301 Ignition Coil Cylinder 1 Circuit High Voltage 6.24 DTC P0351, P0352, P0353, P0354,
P0355, P0356, P2300, P2301, P2303,
P2304, P2306, P2307, P2309, P2310,
P2312, P2313, P2315 or P2316
P2303 Ignition Coil Cylinder 2 Circuit Low Voltage 6.24 DTC P0351, P0352, P0353, P0354,
P0355, P0356, P2300, P2301, P2303,
P2304, P2306, P2307, P2309, P2310,
P2312, P2313, P2315 or P2316
P2304 Ignition Coil Cylinder 2 Circuit High Voltage 6.24 DTC P0351, P0352, P0353, P0354,
P0355, P0356, P2300, P2301, P2303,
P2304, P2306, P2307, P2309, P2310,
P2312, P2313, P2315 or P2316
P2306 Ignition Coil Cylinder 3 Circuit Low Voltage 6.24 DTC P0351, P0352, P0353, P0354,
P0355, P0356, P2300, P2301, P2303,
P2304, P2306, P2307, P2309, P2310,
P2312, P2313, P2315 or P2316
P2307 Ignition Coil Cylinder 3 Circuit High Voltage 6.24 DTC P0351, P0352, P0353, P0354,
P0355, P0356, P2300, P2301, P2303,
P2304, P2306, P2307, P2309, P2310,
P2312, P2313, P2315 or P2316
P2309 Ignition Coil Cylinder 4 Circuit Low Voltage 6.24 DTC P0351, P0352, P0353, P0354,
P0355, P0356, P2300, P2301, P2303,
P2304, P2306, P2307, P2309, P2310,
P2312, P2313, P2315 or P2316
Page 6C1-2–78