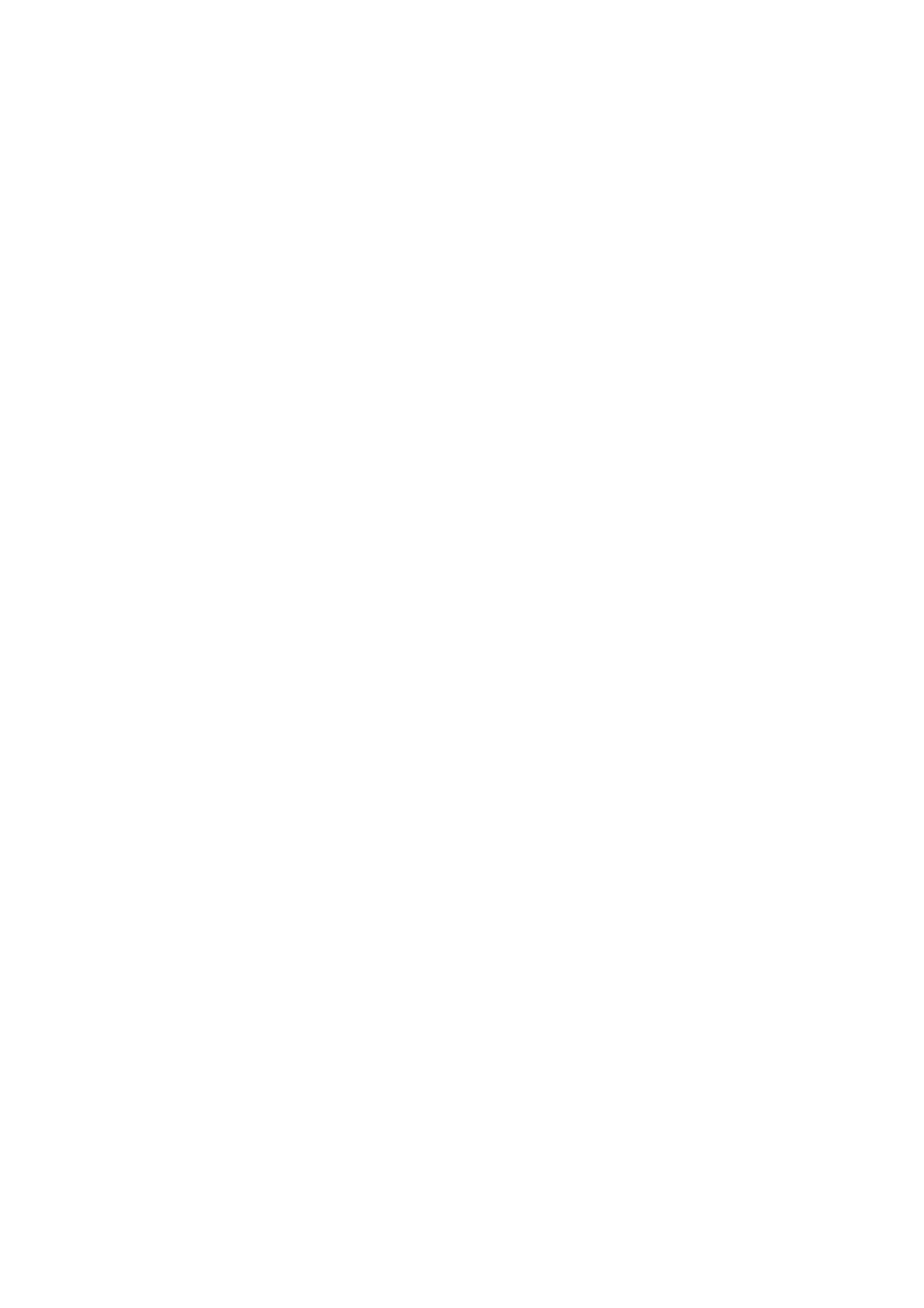
4.5 HYDRAULIC VALV E LIFTERS
Hydraulic valve lifters seldom require attention. The lifters are extremely simple in design, readjustments are not
necessary and servicing of the lifters requires only that care and cleanliness be exercised in the handling of parts.
The easiest method for locating a noisy valve lifter is by use of a piece of garden hose near the end of each inlet
and exhaust valve with the other end of the hose to the ear.
In this manner, the sound is localised, making it easy to determine which lifter is at fault.
Another method is to place a finger on the face of the valve spring retainer. If the lifter is not functioning properly, a
distinct shock will be felt when the valve returns to its seat.
The general types of valve lifter noise are as follows:
1. Momentary noise when car is started:
This condition is normal. Oil drains from the lifters which are holding the valves open when the engine is not
running. It will take a few seconds for the lifter to fill after the engine has started.
2. Intermittently noisy on idle only, disappearing when engine speed is increased:
Intermittent clicking may be an indication of a flat or pitted ball, or it may be caused by dirt.
Correction: Clean the lifter and inspect. If ball is defective, replace lifter.
3. Noisy at slow idle or with hot oil, quiet with cold oil or as engine speed is increased:
Insert a 0.375 mm feeler gauge between the rocker arm and valve stem. If noise momentarily disappears and
then re-appears after a few seconds, the lifter leak-down rate is too fast.
Correction: The lifter must be replaced.
4. Noisy at high car speeds and quiet at low speeds.
a. High oil level. Oil level above the FULL mark allows crankshaft counterweights to churn the oil into foam.
When foam is pumped into the lifters, they will become noisy since a solid column of oil is required for
proper operation.
Correction: Drain oil until proper level is obtained.
b. Low oil level. Oil level below the ADD mark allows the pump to pump air at high speeds which results in
noisy lifters.
Correction: Fill until proper oil level is obtained.
c. Oil pan bent on bottom or oil suction screen and pipe loose, repair or replace as necessary.
5. Noisy at idle becoming louder as engine speed is increased to 1500 rpm.
a. This noise is not connected with lifter malfunction and is caused by one or more of the following:
- Badly worn or scuffed valve tip and rocker arm pad.
- Excessive valve stem to guide clearance.
- Excessive valve seat run-out.
- Off square valve spring.
- Off square rocker arm pad.
- Excessive valve face run-out.
- Valves noisy regardless of engine speed.
This condition can be caused by foreign particles or valve lash.
Check for lash by turning engine so the piston in that cylinder is on top dead centre of firing stroke. If valve lash
is present, the pushrod can be freely moved up and down a certain amount with rocker arm held against valve.
If this occurs, replace suspected valve lifters
Valve lash indicates one of the following:
a. Worn pushrod.
b. Worn rocker arm.
c. Lifter plunger stuck in down position due to dirt or carbon.
d. Faulty lifter.
When checking the above items
1. Look at the upper end of pushrod. Excessive wear of the spherical surface indicates one of the following
conditions:
a. Improper hardness of pushrod ball. The pushrod and rocker arm must be replaced.
b. Improper lubrication of pushrod and rocker arm. The oiling system to the pushrod should be checked.
2. If pushrod appears in good condition and has been properly lubricated, replace rocker arm and recheck for
valve lash.
3. If valve lash exists and pushrod and rocker arm are OK, trouble is in the lifter. Lifter should be replaced.