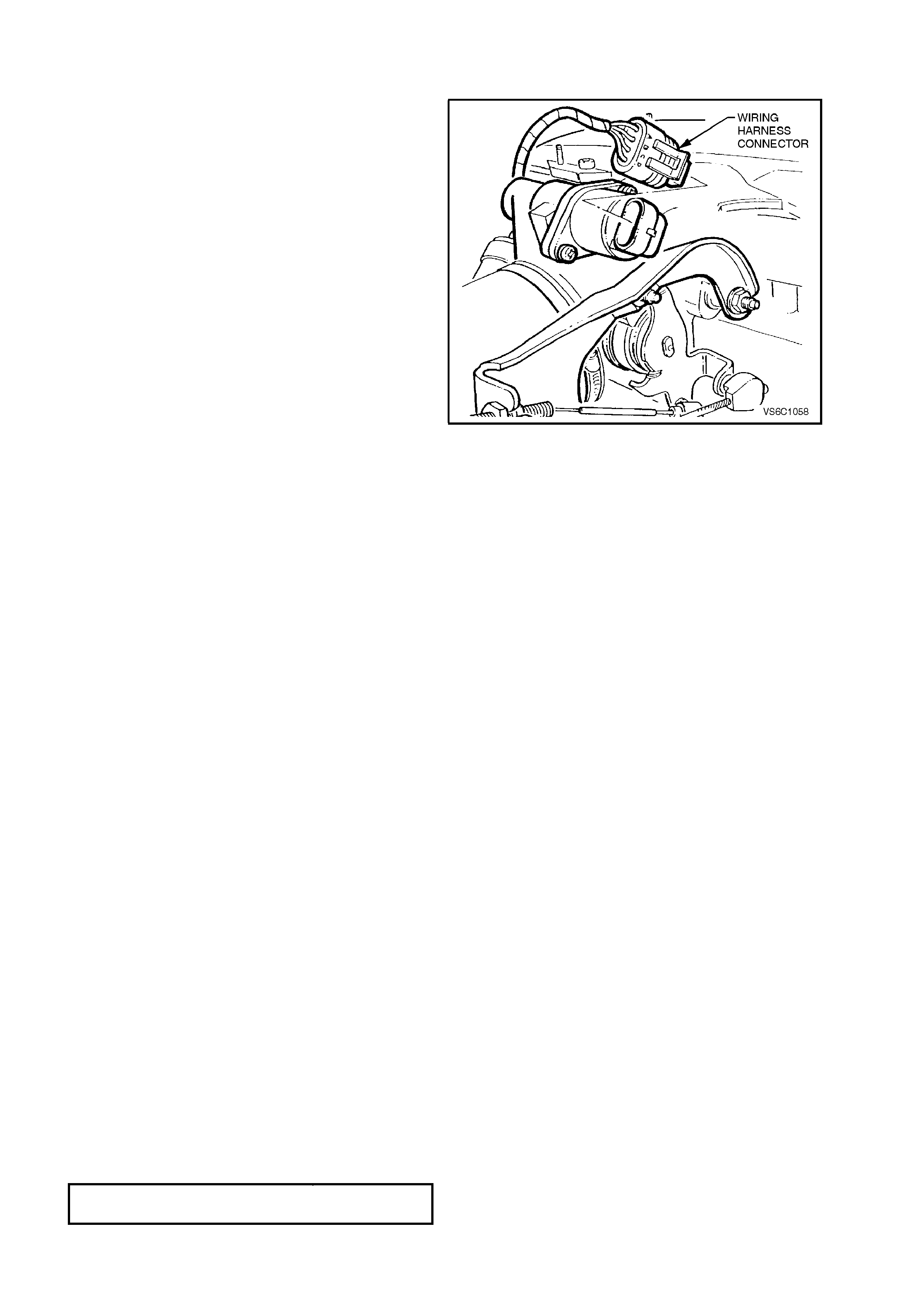
CHECK OR RESET
1. Before performing this procedure, perform the
On-Board Diagnostic System Check, and
follow it upto and including step 9 action
column. Refer to Chart A - On Board
Diagnostic System Check, in Section 6C1-2A,
DIAGNOSTIC CHARTS – V6 ENGINE in the
VT Ser vice Inf ormation. If values are norm al or
within typical ranges proceed to step 2 below
2. Ensure that the IAC system is functioning
properly. Refer to Diagnostic Chart A-7.1 V6
PCM - IAC system in Section 6C1-2A,
DIAGNOSTIC CHARTS - V6 ENGINE in the
VT Service Information, and follow it to step
3"NO TROUBLE FOUND WITH IAC
SYSTEM".
3. Remove four dome nuts securing the engine
dress cover assembly to the inlet manifold
studs, lift off and remove the cover assembly.
IMPORTANT: Verify that the throttle cable and
throttle linkage are not binding. The throttle lever
attached to the throttle butterfly shaft must be able
to open fully, and shut fully and freely every time
the accelerator pedal is fully depressed and slowly
released. If throttle cable adjustment is required,
refer to THROTTLE CABLE in this Section of the
VT Service Information.
4. Engine must be at normal operating
temperature (above 90 degrees C), it is
preferable to achieve by driving the vehicle for
at least 15 minutes, before continuing.
5. Set parking brake and block drive wheels.
Ensure transmission is in `Park' (auto) or
neutral (manual).
6. Ignition "ON," ensure that all electrical loads
are turned "OFF," i.e. air conditioning, lights
etc. "OFF."
7. Connect TECH 2 to DLC and select:
Diagnostics / Appropriate Model Year / VT
Comm odore / Engine / V6 / Confirm Prom I.D. etc.
/ Misc ellaneous tests / IAC system / Bas e Idle / and
follow TECH 2 instructions.
IMPORTANT:If engine stalls while following TECH
2 instructions, turn the throttle stop screw ½ a turn
in the clockwise direction and repeat the base idle
checking procedure. If adjustment of the throttle
stop screw is necessary, adjust screw to obtain an
engine speed of 450 – 550 RPM.
Figure 6C1-3-26 IAC Valve Harness Removed
8. Reset IAC. To do this, either:
Start engine, use TECH 2 scan tool and select
IAC reset, and follow TECH 2 instructions.
-OR-
Start engine, allow engine to run for 5 seconds,
then turn engine "OFF" for 10 seconds to
“Reset” the IAC valve.Restart engine and check
for proper idle.
9. Reinstall engine dress cover to the inlet
manifold, ensuring that stud grommets in the
dress cover remain in place. Tighten securing
dome nuts to the correct torque.
ENGINE DRESS COVER SECURING
DOME NUT TO INLET MANIFOLD
TORQUE SPECIFICATION
4 - 6 Nm