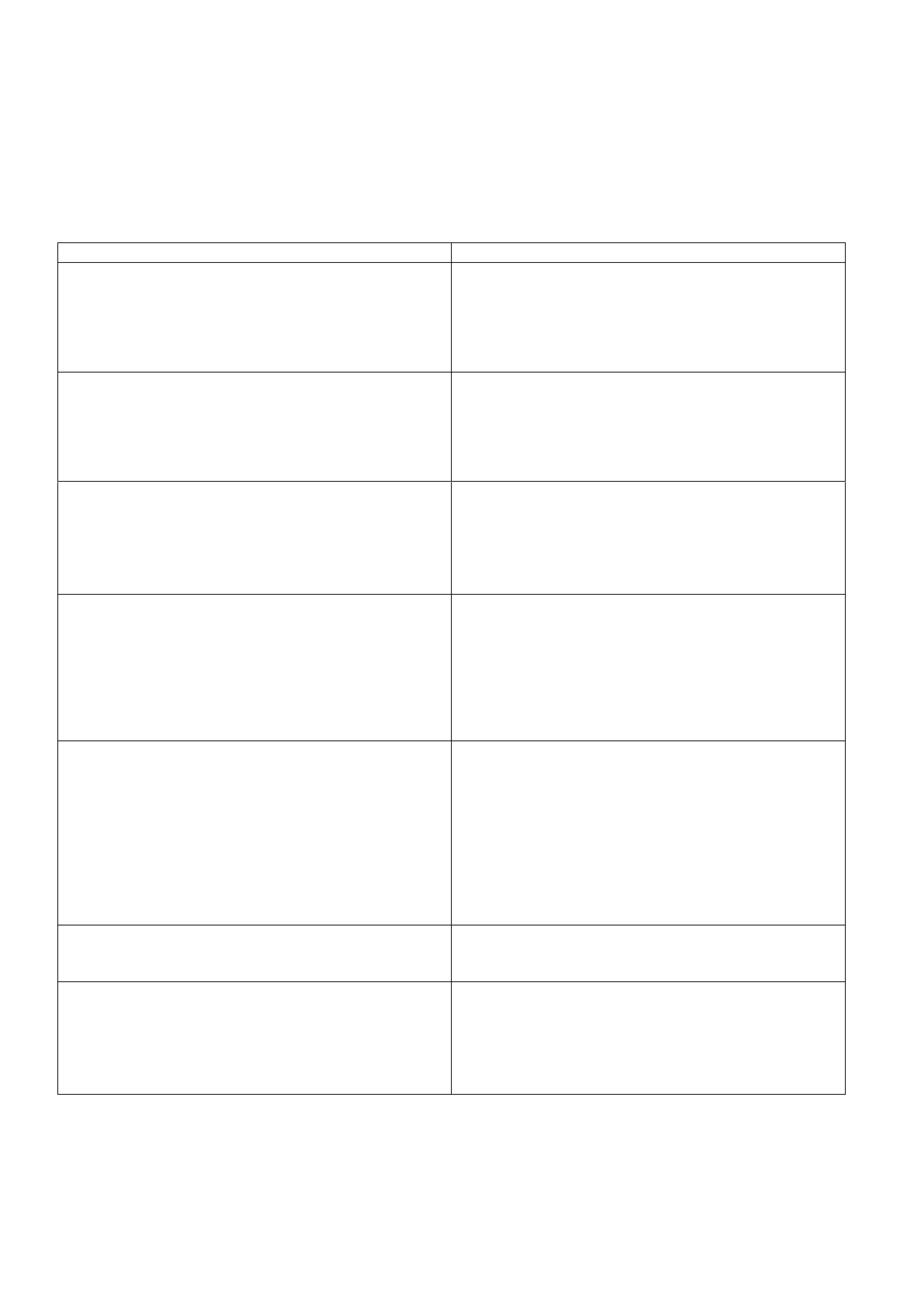
2.12 SYMPTOM DIAGNOSIS
The following table consists of seven diagnostic categories that are located in the left-hand column. Using this
column, choose the appropriate category based on the operating conditions of the vehicle or transmission. The
tables that follow, provide more specific information relating to each of the symptoms listed.
After selecting a category, use the right-hand column to locate the specific symptom diagnostic information.
Important: The Functional T est Procedure should be performed before beginning an y diagnosis. If this procedure
has not already been performed, refer to Functional Test Procedure, in this Section.
SYMPTOM DIAGNOSIS TABLE
Diagnostic Category Diagnostic Information
FLUID DIAGNOSIS
This category contains the following topics:
• Fluid condition (appearance, contaminants, smell,
overheating)
• Line pressure (high or low)
• Fluid leaks
• Refer to 2.3 Transmission Fluid Checking Procedure, in
this Section.
• Refer to Oil Pressure High or Low.
• Refer to Fluid Leak Diagnosis (procedure).
• Refer to Oil Out the Vent .
• Refer to Front Oil Leak.
Noise and Vibration Diagnosis
This category contains the following topics:
• Ratcheting noise
• Noise (drive gear, final drive, whine, growl, rattle, buzz,
popping)
• Vibration
• Refer to Ratcheting Noise.
• Refer to Vibration in Reverse and Whining Noise in Park.
Range Performance Diagnosis
This category contains the following topics: Drives in Neutral
• No Park
• No Reverse
• No Drive
• No engine braking
• Refer to Drives in Neutral.
• Refer to No Park.
• Refer to No Reverse or Slips in Reverse.
• Refer to No Drive in All Ranges.
• Re fer to No Drive in Drive Range.
• Refer to No Overrun Braking - Manual 3-2-1.
SHIFT QUALITY (FEEL) DIAGNOSIS
This category contains the following topic:
• Harsh, soft or slipping shifts
• Harsh, soft or delayed engagement
• Shift shudder, flare or tie-up
• Refer to Harsh Shifts.
• Refer to Slipping or Rough 1-2 Shift.
• Refer to No 2-3 Shift or 2-3 Shift Slips, Rough or
Hunting.
• Refer to No 3-4 Shift, Slips or Rough 3-4 Shift.
• Refer to Harsh Garage Shift.
• Refer to Dela y in Drive and Reverse.
• Refer to 3-2 Flare or Tie-Up.
SHIFT PATTERN
This category contains the following topics:
• One forward gear only
• Two forward gears only gear missing or slipping
• No upshift or slipping upshift
• No downshifts
• Non-First gear start
• Refer to 1st Gear Range Only - No Upshift.
• Refer to Third Gear Only.
• Refer to 2nd/3rd Gear Only or 1st/4th Gears Only.
• Refer to Slips in 1st Gear.
• Refer to Slipping or Rough 1-2 Shift.
• Refer to No 2-3 Shift or 2-3 Shift Slips, Rough or
Hunting.
• Refer to No 3-4 Shift, Slips or Rough 3-4 Shift.
• Refer to No Part Throttle or Delayed Downshifts.
• Refer to 2nd Gear Start.
SHIFT SPEED DIAGNOSIS
This category contains the following topic:
• Inaccurate or inconsis tent sh ift point s
• Refer to Inaccurate Shift Points.
TORQUE CONVERTER DIAGNOSIS
This category contains the following topics:
• Torque converter diagnosis
• TCC does not apply
• TCC does not release
• TCC apply/release quality
• Refer to Torque Converter Diagnosis Procedure.
• Re fer to No TCC Apply.
• Re fer to No TCC Release.
• Refer to Torque Converter Clutch Shudder.