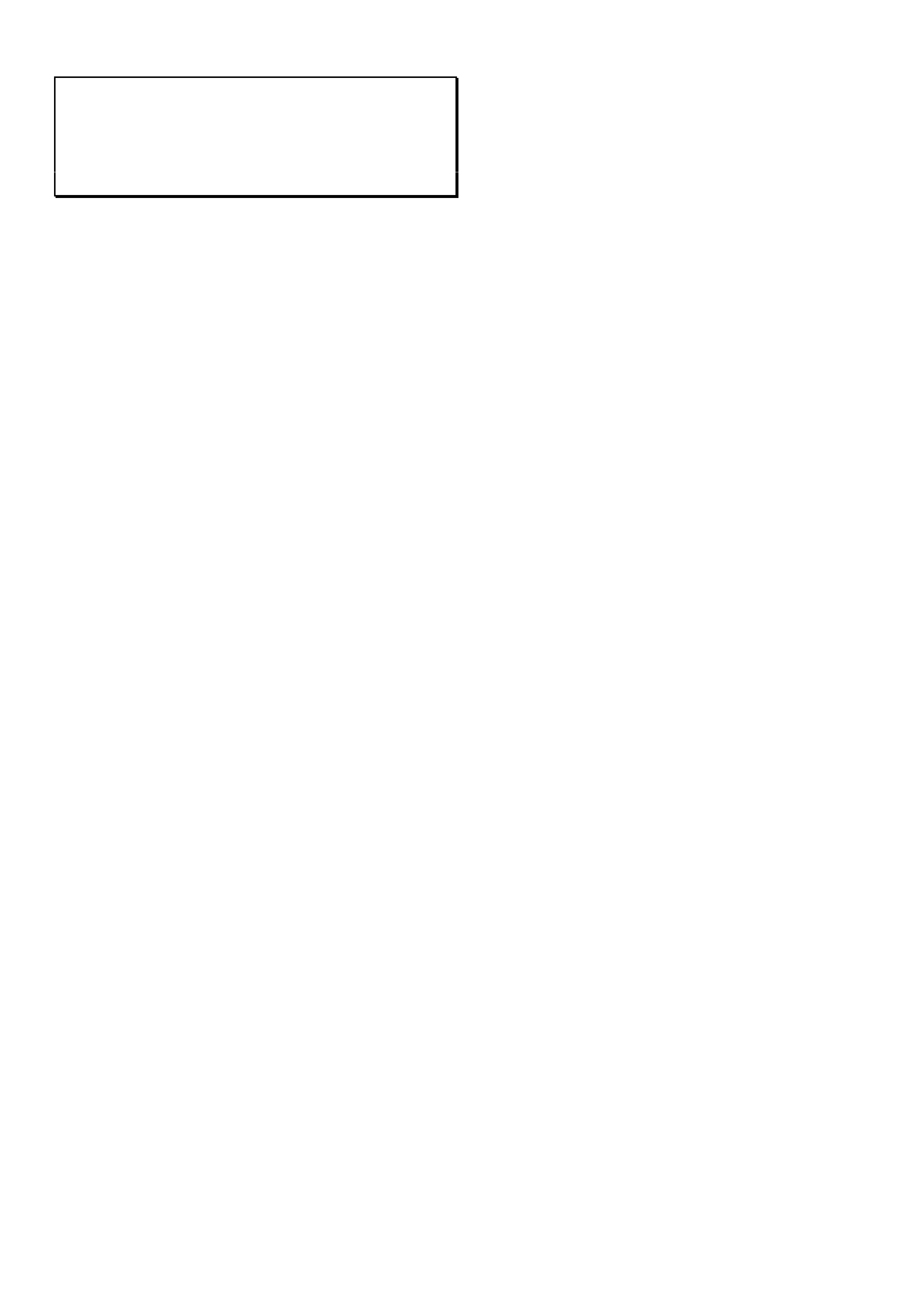
HOLDEN SERVICE TECHLINE_____________________________________________________________________APRIL, 2002
12
Engine Oil Consumption Information
All
(GROUP 6A) TL260-0203
This Techline is provided for general information.
All engines require oil to lubricate and protect the
load bearing and internal moving parts from wear
including cylinder walls, pistons and piston rings.
When a piston moves down its cylinder, a thin film
of oil is left on the cylinder wall. During the power
stroke, part of this oil layer is consumed in the
combustion process. As a result, varying rates of
oil consumption are accepted as normal in all
engines.
Many external factors, such as owner driving habits
and vehicle maintenance, can affect the rate of oil
consumption.
The following are some important items affecting
oil consumption which must be taken into account
when evaluating customer complaint vehicles.
Gasket and External Leaks
Inspect the oil pan and engine covers for leakage
due to over-tightened, damaged, or out of place
gaskets. Inspect oil lines and fittings for signs of
leakage.
Improper Reading of the Oil Level Indicator
(Dipstick)
Verify that the dipstick tube is fully seated in the
block. When checking the oil level, make sure the
dipstick is wiped clean before taking an oil level
reading and fully
depress the dipstick until the shoulder bottoms out
on the dipstick tube. The dipstick should be the
proper part number for the engine/vehicle that is
being checked.
Not Waiting Long Enough After Running Engine
to Check Oil Level
The vehicle should be allowed to sit for at least 10
minutes after the engine has been shut off, before
taking an oil level reading to assure the oil has had
enough time to drain back into the crankcase. In
order to ensure accurate results, the temperature
of the oil should be close to the same temperature
as the last time the oil level was checked.
Improper Oil Fill After an Oil Change
Following an oil change, verify that the proper
amount and type of oil was put in the engine and
that the oil level on the dipstick is not above the full
mark or below the add marks. Refer to the
Owner's Manual or Service Manual for information
on recommended oil quantity, viscosity, and
quality.
High Speed or High RPM Driving
Continuous driving at high speeds/high RPMs may
increase oil consumption. Because this may not
always be an everyday occurrence, it is hard to
determine exactly how much the oil economy will
be affected.
Towing or Heavy Usage
Towing a trailer will increase oil consumption and
may cause oil consumption to fall below the normal
accepted rate referenced in this bulletin for an
unloaded vehicle in a personal use application.
Large frontal area trailers will further increase the
work required from the engine, especially at
highway speeds, and thus increases the rate of oil
consumption.
Crankcase Ventilation System
Verify that the positive crankcase ventilation (PCV)
system is operating properly. Incorrect PCV
valves, blockages, restrictions, or damage to the
PCV system can result in increased oil use.
Oil Dilution (Fuel and Water)
On vehicles that are usually driven short distances,
less than 8 km, especially in colder weather,
unburned fuel and condensation generated from
cold engine operation may not get hot enough to
evaporate out of the oil. When this occurs, the
dipstick may indicate that the oil level is over-full.
Subsequent driving on a trip where the engine is at
normal operating temperature for 30 minutes or
more, will vaporize excess moisture and fuel, and
may give the customer the impression of excessive
oil consumption if the oil level is checked
immediately after.