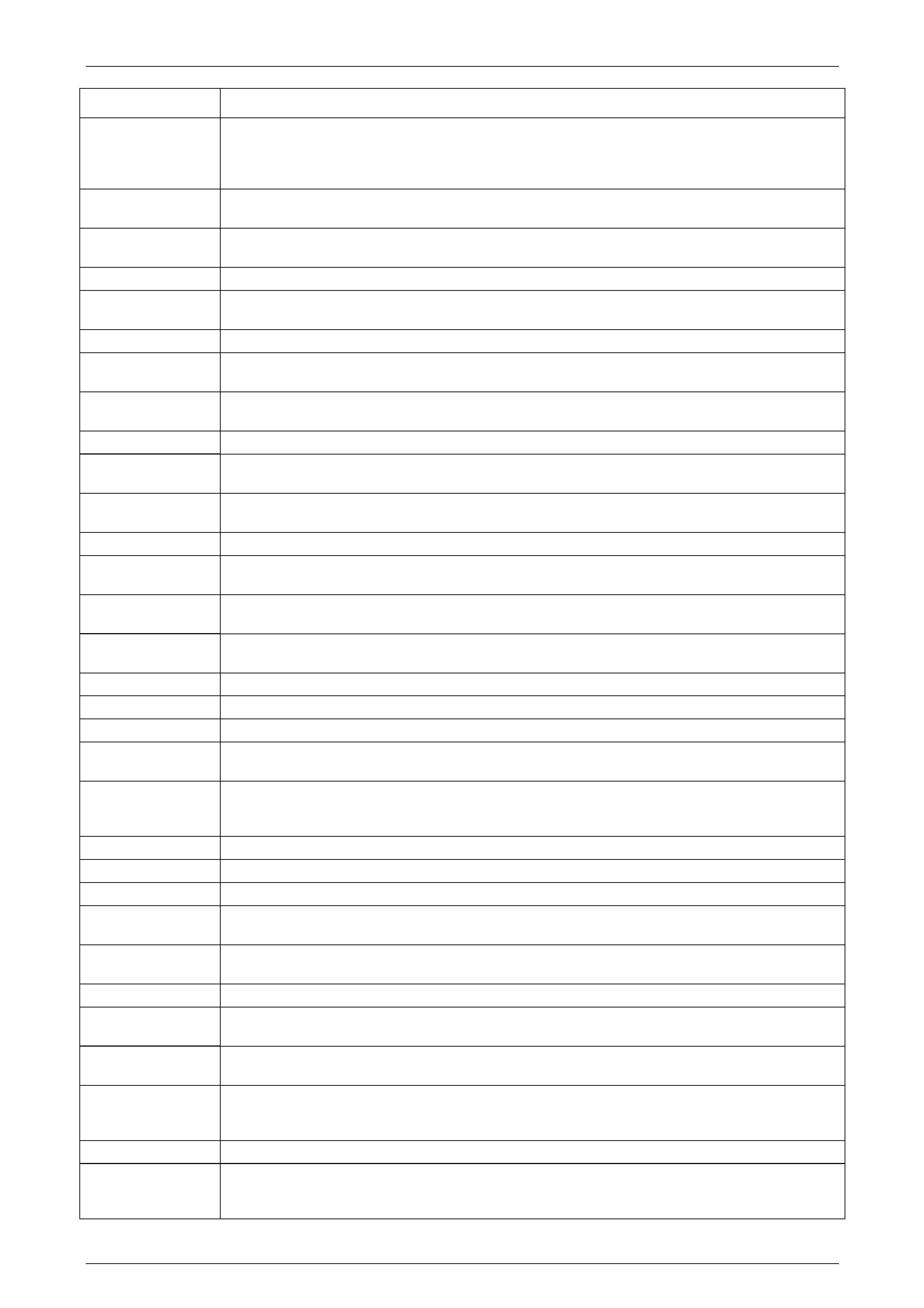
Engine Management GEN IV V8 – General Information Page 6C4-1–42
Page 6C4-1–42
Abbreviation Description
EVAP Evaporative emission control system. Used to prevent fuel vapours from the fuel tank from
entering into the atmosphere. The vapours are stored in a canister that contains an activated
charcoal element. The fuel vapours are purged from the canister into the manifold to be burned in
the engine.
GM LAN General Motors Local Area Network – A type of serial data for communication b etween electronic
devices.
Fuse A thin metal strip which melts when excessive current flo ws through it, creating an open circuit
and protecting a circuit from damage.
HC Hydrocarbon. Result of unburned fuel produced by incomplete combustion.
Heated O2 Sensor Heated Oxygen Sensor. A device located in the exhaust system that provides a variable voltage to
the ECM based on the oxygen content of exhaust gas
Heavy Throttle Approximately 3/4 of accelera tor pedal travel (75% throttle position)
IAT Sensor Intake Air Temperature senso r . A device that provides a variable voltage to the ECM based on the
temperature of air entering the intake system.
Ideal Mixture The air / fuel ratio which provides the best performance, while maintaining maximum conversion of
exhaust emissions, typically 14.7 to 1 on spa rk ignition engines
IGN Ignition
Inputs Information from sensors (MAF, TP, etc.) and switches (A/ C request, etc.) used by the ECM to
determine how to control its outputs.
Intermittent An electrical signal that occurs no w and then; not continuously. In electrical circuits, refers to
occasional open, short, or ground in a circuit
Light Throttle Approximately 1/4 of accelerator peda l travel (25% throttle position)
Low A voltage less than a specific threshold. Operates the same as a ground and may, or may not, be
connected to chassis ground.
MAF Sensor Mass Air Flow Sensor. A device that provides a variable voltage to the ECM based on the amount
of air flow entering in the intake system.
MIL Malfunction Indicator Lamp, located in the instrument cluster, will illuminate if the engine starts
operating outside the pre-programmed emission parameters
Medium Throttle Approximately 1/2 of accelerator pedal travel (50% throttle position)
N.C Normally Closed. Switch contacts that are closed when they are in the n ormal operating position
N.O Normally Open. Switch contacts that are normally open when in the normal operating position
NOx Nitrogen Oxide. One of the pollutants found in spark ig nition engine exhaust that is formed from
normal combustion and increases in severity with combustion temperature.
O2 Sensor Oxygen Sensor. A device loc ated in th e exhaust system that provides a variable voltage to the
ECM based on the oxygen content of exhaust gas.
May also include a heating circuit to provide faster initial warm-up (Heated O2 sensor).
OBD On Board Diagnostic
Open Loop ECM control of the fuel control system without the use of the oxygen sensor signal.
Output Functions that are controlled by the ECM, typically these can include solenoids and relays, etc.
PCV Positive Crankcase Ventilation. Method of re burning crankcase fumes rather than passing them
directly into the atmosphere
PIM Powertrain Interface Module – The PIM acts as a communication trans lator between the ECM and
other on-board controllers tha t use a different serial data protocol.
PM Permanent Magnet
PWM Pulse Width Modulated. A digital signal turned on and off for a percentage of availabl e cycle time.
A signal that is 30% on and 70% off would be termed a 30% on PWM signal.
Quad Driver A transistor in the ECM capable of operating four separate o utputs. Outputs can be either on-off or
pulse width modulated.
RAM Random Access Memory. A microprocessor c an write into or read from this memory as needed.
This memory is volatile and needs a constant power supply to be retained. If the power is lost or
removed, RAM data is lost.
RPM Revolutions Per Minute
Serial Data Serial data is a series of rapidly changing voltage signals pul s ed from high to low. These signals
are typically 5 volts (UART), 7 volts (Class II), and 12 or 0 volts (high or low) and are transmitted
through a wire often referred to as the Serial Data Circuit.