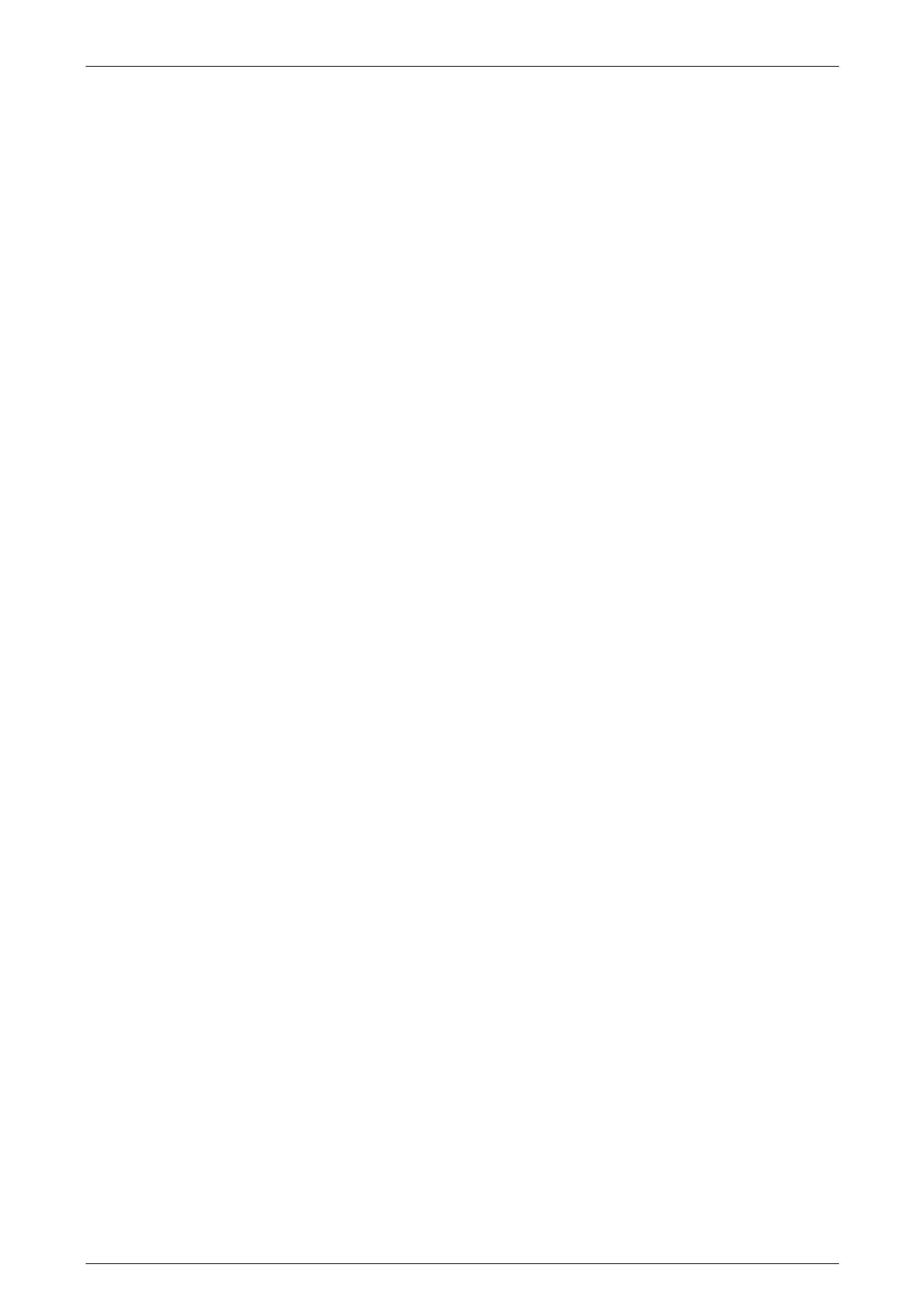
Service and Park Braking System 5A – 2
2.9 Park Brake Lever.................................................................................................................................................. 32
Remove................................................................................................................................................................. 32
Reinstall................................................................................................................................................................ 33
2.10 Park Brake Warning Lamp Switch...................................................................................................................... 34
Remove................................................................................................................................................................. 34
Inspect .................................................................................................................................................................. 34
Reinstall................................................................................................................................................................ 34
2.11 Front Park Brake Cable ....................................................................................................................................... 35
Remove................................................................................................................................................................. 35
Reinstall................................................................................................................................................................ 35
2.12 Rear Park Brake Cab le/s ..................................................................................................................................... 37
Remove................................................................................................................................................................. 37
Reinstall................................................................................................................................................................ 38
2.13 Front Brake H ose................................................................................................................................................. 39
Remove................................................................................................................................................................. 39
Reinstall................................................................................................................................................................ 39
2.14 Rear Caliper Brake Hose..................................................................................................................................... 41
Remove................................................................................................................................................................. 41
Reinstall................................................................................................................................................................ 42
2.15 Rear Brake Hose – All Except Live Axle Models............................................................................................... 43
Remove................................................................................................................................................................. 43
Reinstall................................................................................................................................................................ 44
2.16 Rear Brake Hose/s – L ive Axle Models .............................................................................................................. 45
Remove................................................................................................................................................................. 45
All Live Axle Models......................................................................................................................................... 45
All Except AWD & Live Axle............................................................................................................................. 45
AWD & Live Axle Only...................................................................................................................................... 46
Reinstall................................................................................................................................................................ 47
All Live Axle Models......................................................................................................................................... 47
All Except AWD & Live Axle............................................................................................................................. 47
AWD & Live Axle Only...................................................................................................................................... 47
All Live Axle Models......................................................................................................................................... 47
2.17 Brake Booster Hose & Valve Assembl y – V6 Eng i ne........................................................................................ 48
Replace................................................................................................................................................................. 48
2.18 Brake Booster Hose & Valve Assembl y – V8 Eng i ne........................................................................................ 49
Replace................................................................................................................................................................. 49
2.19 Load Sensing Proportioning Valve (LSPV)........................................................................................................ 50
Remove................................................................................................................................................................. 50
All VZ Models With LSPV................................................................................................................................. 50
Utility Models.................................................................................................................................................... 50
AWD & Live Axle.............................................................................................................................................. 51
Reinstall................................................................................................................................................................ 52
All LSPV Applications....................................................................................................................................... 52
Rear Brake Pipe Layout - Utility W ithout ABS.................................................................................................. 53
2.20 Brake Fluid Level Switch..................................................................................................................................... 54
Test ....................................................................................................................................................................... 54
Replace................................................................................................................................................................. 54
3 Major Service Operations....................................................................................................................55
3.1 Master Cylinder.................................................................................................................................................... 55
Remove................................................................................................................................................................. 55
Reinstall................................................................................................................................................................ 56
3.2 Brake Master Cylinder Reservoir........................................................................................................................ 57
Replace................................................................................................................................................................. 57
3.3 Brake Booster ...................................................................................................................................................... 58
Remove................................................................................................................................................................. 58
Reinstall................................................................................................................................................................ 59
5A – 2