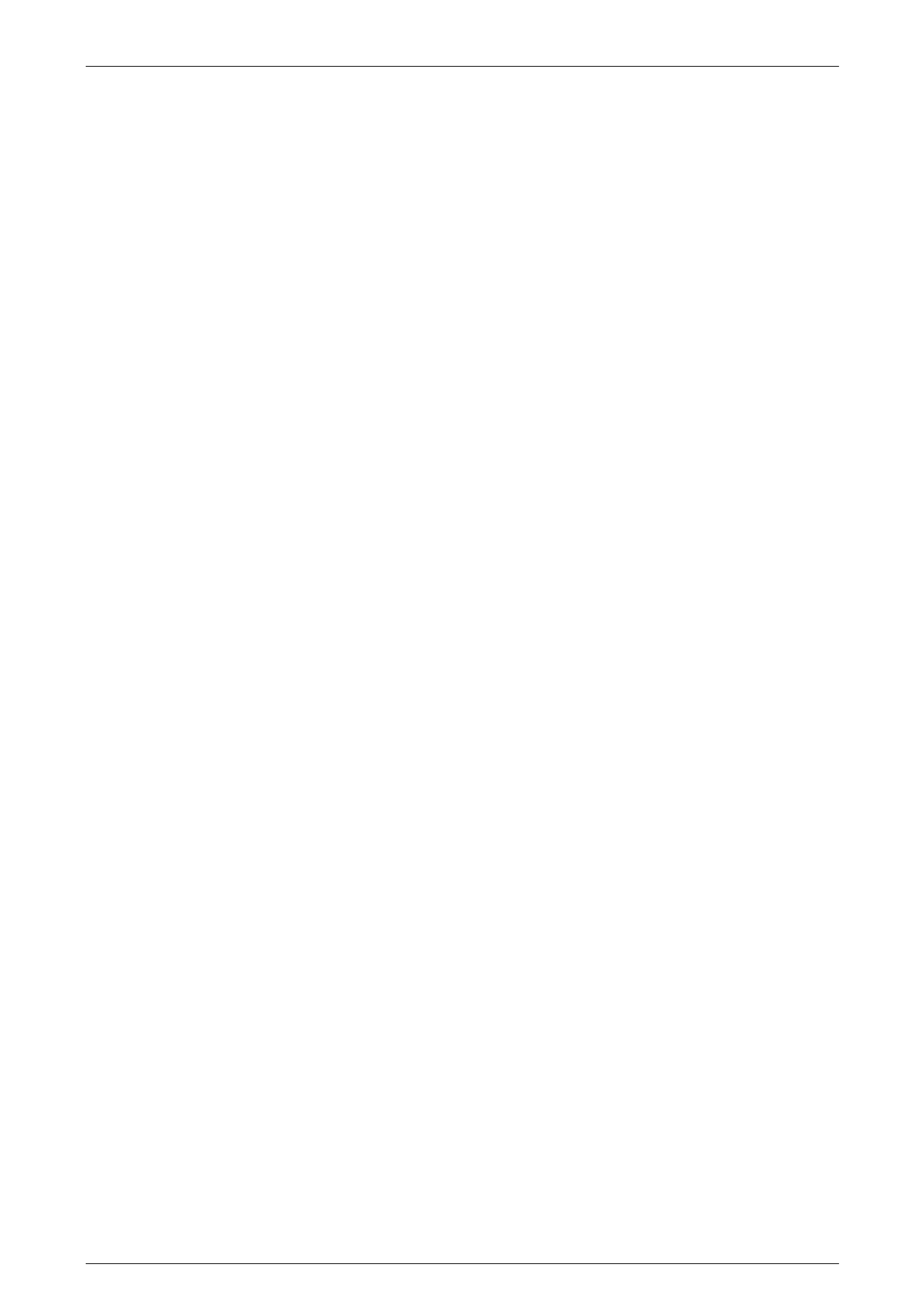
Engine Management – V6 – Service Operations Page 6C1-3–2
Air Cleaner Lower Housing Assembly ............................................................................................................... 27
Remove............................................................................................................................................................ 27
Reinstall ........................................................................................................................................................... 27
3.5 Barometric Pressure Sensor............................................................................................................................... 28
Remove................................................................................................................................................................. 28
Reinstall................................................................................................................................................................ 28
3.6 Camshaft Position Actuator Solenoid................................................................................................................ 29
Bank 1 (RHS) ........................................................................................................................................................ 29
Remove............................................................................................................................................................ 29
Reinstall ........................................................................................................................................................... 30
Bank 2 (LHS)......................................................................................................................................................... 31
Remove............................................................................................................................................................ 31
Reinstall ........................................................................................................................................................... 32
Test ....................................................................................................................................................................... 33
Resistance Inspection ...................................................................................................................................... 33
Functional Test................................................................................................................................................. 33
3.7 Camshaft Position Sensor .................................................................................................................................. 34
Bank 1 (RHS) ........................................................................................................................................................ 34
Remove............................................................................................................................................................ 34
Reinstall ........................................................................................................................................................... 35
Bank 2 (LHS)......................................................................................................................................................... 36
Remove............................................................................................................................................................ 36
Reinstall ........................................................................................................................................................... 37
3.8 Crankshaft Position Sensor................................................................................................................................ 38
Remove................................................................................................................................................................. 38
Test ....................................................................................................................................................................... 39
Resistance Check ............................................................................................................................................ 39
Reinstall................................................................................................................................................................ 39
3.9 Engine Coolant Temperature Sensor................................................................................................................. 40
Remove................................................................................................................................................................. 40
Test ....................................................................................................................................................................... 41
Resistance Check ............................................................................................................................................ 41
Reinstall................................................................................................................................................................ 42
3.10 Engine Control Module........................................................................................................................................ 43
Remove................................................................................................................................................................. 43
Reinstall................................................................................................................................................................ 44
ECM Reset ............................................................................................................................................................ 45
3.11 Engine Control Module Bracket Assembly........................................................................................................ 46
Remove................................................................................................................................................................. 46
Reinstall................................................................................................................................................................ 46
3.12 Engine Oil Level and Temperature Sensor........................................................................................................ 47
Remove................................................................................................................................................................. 47
Test ....................................................................................................................................................................... 48
Engine Oil Level Sensor Check........................................................................................................................ 48
Reinstall................................................................................................................................................................ 48
3.13 Engine Oil Pressure Sensor................................................................................................................................ 49
Remove................................................................................................................................................................. 49
Reinstall................................................................................................................................................................ 50
3.14 Evaporative Emission Canister Purge Valve..................................................................................................... 51
Remove................................................................................................................................................................. 51
Test ....................................................................................................................................................................... 52
Resistance Check ............................................................................................................................................ 52
Functional Test................................................................................................................................................. 52
Reinstall................................................................................................................................................................ 53
3.15 Fuel Rail Assembly .............................................................................................................................................. 54
Remove................................................................................................................................................................. 54
Disassemble......................................................................................................................................................... 55
Fuel Injector ..................................................................................................................................................... 55
Fuel Injector Wiring Harness Assembly............................................................................................................ 57
Reinstall................................................................................................................................................................ 59
Page 6C1-3–2